What is a slicing tool? Examples, classifications and substances
- Share
- Issue Time
- Mar 30,2022
Summary
Machining is a manufacturing operation wherein extra material is steadily removed with the aid of shearing from a preform in the form of chips. A inflexible, inflexible, wedge-fashioned tool called a slicing tool is used to compress the working cloth, thereby shearing off excess layers of material.
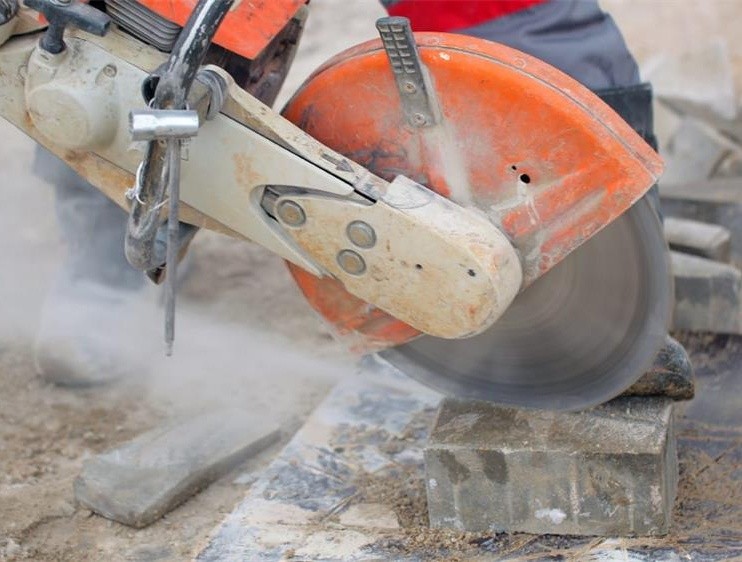
Machining is a manufacturing operation wherein extra material is steadily removed with the aid of shearing from a preform in the form of chips. A inflexible, inflexible, wedge-fashioned tool called a slicing tool is used to compress the working cloth, thereby shearing off excess layers of material.
So the cause of a reducing tool (additionally referred to as a cutter) is to compress a selected layer of operating cloth to shear it away. Therefore, the cutter must have a pointy wedge shape for easy and efficient elimination of material that requires minimal electricity. At the identical time, the tool fabric must be hard enough to resist the extreme friction that takes place during machining. The following sections are mentioned at the side of definitions and examples, uses, diverse characteristics, names, substances, and classification of slicing tools.
What's a reducing tool?
A reducing device is a wedge-formed and sharp-edged tool used to take away excess layers of material from a workpiece with the aid of shearing all through machining to reap the preferred form, length, and precision. It's far rigidly hooked up at the device device. The relative speed among the workpiece and the reducing tool is also provided by using diverse mechanical and different devices used for the cutting motion.
Device example
A tool is essentially a tool utilized in machining operations. Numerous machining operations use one of a kind tools, so these gear can go with the aid of distinctive names depending at the software. A list of generally used slicing gear is provided beneath.
Single factor turning gear - equipment for turning operations on lathes
Drill bit - a tool used for drilling operations on a drilling or lathe or milling system
Milling cutter (or milling cutter) - a tool used for milling operations on a milling machine
Fly cutters - tools for fly milling operations on milling machines
Shaping Machines - tools for Shaping Operations in Shaping Machines
Planer - a tool used for planing paintings in a planer
Uninteresting bars - tools used for boring operations on drilling or dull machines
Reamers - gear for reaming operations on drilling machines
Broach - a tool for broaching operations in a broaching gadget
Hob - tool for hobbing operations in tools hobbing machines
Grinding Wheel - Abrasive tool used for grinding operations on a grinding device.
Geometric functions and device names
The geometry of the slicing device includes numerous planes and the inclination and orientation of the tool's reducing edge in addition to the nostril radius. Knife nomenclature basically refers to showing diverse capabilities of a knife in a symbolic however standardized manner. There are various device designation systems, every with a selected fashion for expressing those traits. Among numerous systems, the usually used turning tool designation structures are indexed underneath.
Tool in hand gadget
American standards association (ASA) system
Orthogonal Rake system (ORS) or ISO legacy device
Normal Rake device (NRS) or ISO New system
Most Rake device (MRS)
Tool material
All through machining, a portion of the slicing device is in bodily touch with the workpiece and therefore studies severe reducing temperatures and consistent friction. The fabric of the cutting tool must have the ability to resist such excessive slicing temperatures and reducing forces. Each device material need to own positive properties which include excessive hardness, excessive warm hardness, excessive strength, high melting point and chemical inertness even at excessive cutting temperatures. Normally of thumb, the hardness of the device cloth must be as a minimum 1.5 times the hardness of the workpiece for smooth slicing movement.
Suitable coatings can also be applied to the device to improve numerous favored properties. However, coating gear do now not allow smooth re-polishing with the aid of grinding while the edge wears out after extended use. Blade-based equipment at the moment are to be had, in which small interchangeable blades may be connected or clamped to big shanks. These inserts perform reducing action and therefore wear out gradually. Whilst the wear and tear exceeds the allowable restriction, the blade can be replaced with a new one, and the shank can be reused. Indexed beneath are a number of the commonplace tool substances on the market today.
High Speed Steel (HSS)
Tungsten Carbide
ceramics
Cubic Boron Nitride (cBN)
diamond
Classification of tools
Cutting tools can be classified in a number of ways; however, the most common method is based on the number of major cutting edges participating in a cutting action. On this basis, tools can be divided into the following three categories.
Single point cutting tool - This tool has only one major cutting edge participating in the cutting action at a time. Examples include turning tools, boring tools, flying tools, grooving tools, etc.
Dual Point Cutting Tools - As the name suggests, these tools contain two cutting edges that simulate the action of a cut that ultimately participates in a pass. Examples include drill bits (common metal cutting bits with only two flutes).
Multi-point cutting tools - These tools contain more than two main cutting edges that can simultaneously remove material in a single pass. Examples include milling cutters, broaches, gear hobbing cutters, grinding wheels, etc.